Google the term “UK housing shortage” and you get 2m results, concentrating on the supply of homes failing to match demand. But what of that other housing shortage – the lack of labour and materials?
The Construction Products Association’s latest quarterly survey, released in May, shows that 50% of contractors reported difficulties in recruiting carpenters, 46% said the same for plasterers and 30% for bricklayers in the first quarter of 2016.
Meanwhile, there remains a materials shortage. The Department for Business, Innovation & Skills says UK brick manufacturing totalled 2m units in 2015, 7% up on 2014. But a 50% drop in brick imports means the end result remains a shortage. And with last week’s shock Brexit vote, the cost of imported materials could rise sharply as the pound goes down.
The consequences are challenging in the face of increasingly price-sensitive demand for materials.
“It is driving construction costs up and making it difficult to control quality where contractors have stretched their finite resources over too many projects,” says Mark Lebihan, chief operating officer at Hadley Property Group.
His experience is not unique – 42% of housebuilders canvassed by the Construction Products Association reported labour cost increases in the first quarter of 2016 alone.
All this raises the question: while planning, land costs and bureaucratic local authorities are often blamed for long-term slow housebuilding volumes, does the UK have the skills and materials to build more homes even if these obstacles were removed once and for all?
Mark Farmer, chief executive of residential consultancy Cast, has just been asked by the government to investigate what can be done to bring more home-grown workers into the construction industry. Not surprisingly, he has plenty of ideas.
“The issues start with a need for better industry connectivity and presentation at an early age, about 12-plus, in schools,” he says. “Construction needs to reinvent itself as a more modern, technology-embracing career option.
“The current fixation with degree-level education needs to be tempered with a realisation that many are better suited to vocational training, apprenticeships and the like.”
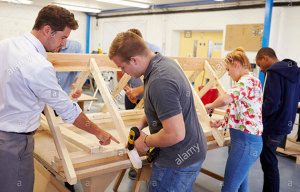
be encouraged to take up apprenticeships
Farmer says the cycle of boom and bust can deter the long-term growth of a skilled housebuilding workforce and he believes that “demand smoothing” through, perhaps, the promotion of institutional clients, is “crucial to instilling longer-term confidence and investment planning”.
Others believe shorter-term measures are needed. Weston Homes, for example, is recruiting school leavers and putting them through apprenticeships, but thinks the government could do more.
”We would like to see all prop-con and engineering graduates educated here staying here,” says the firm’s chairman, Bob Weston. “The rules don’t make it easy. We have to pay overseas students on tier two and tier four visas over £35,000 per annum.
“If this figure was lowered, we could bring in non-EU graduates with the RICS, CIOB and IEng qualifications we are looking for right away.”
Weston has visited China to see first-hand the pros and cons of modular building in a bid to reduce site time and labour requirements, and make construction quality more uniform.
Other companies, such as Hadley Property Group, are already experimenting with this approach.
“Constructing housing volumetrically, off-site, in safer controlled environments, will not only increase speed of construction but also allow a diversified workforce to enter the industry, increasing the labour supply pool considerably,” says Hadley’s Lebihan, who believes that until this system, UK housebuilding has remained broadly unchanged for 30 years.
“We have been working with one volumetric system that uses a temporary production centre erected on site or in a nearby factory shed,” he adds. “Using this across more sites would greatly increase the use of local labour.”
Mat Lown, a partner at consultancy Tuffin Ferraby Taylor, says current build-to-rent construction may encourage modular construction in the UK.
He says a range of BTR schemes now being built at Wembley Park include a 450-unit block where “the programme has been reduced by one year, which equates to £3.5-£4m in rent – a significant cash-flow benefit”.
On top of that, Lown says factory-made elements are normally higher quality than those constructed on site.
So it is clear that on the one hand, the industry recognises the weaknesses of old-school reliance on traditional skills and materials, but on the other hand, it sees the merit in a new approach involving a wider range of skills and construction methods.
The problem is making the leap from the old to the new. It is happening, but not quickly enough to help address the shortages that are currently holding back housebuilding volumes.
Merchant Land
Katherine McCullough, development director at Merchant Land, a niche developer of central London schemes, says skills and labour shortages, plus consequent cost increases, have led her to rethink the typical SME model.
“We have brought construction skills and experience in-house by hiring staff with 20-plus years’ project and site management experience as contractors,” she says. “They, in turn, bring their address books of suppliers, sub-contractors and main contractors.
“We have a much flatter and collaborative approach to delivery at site level. We work closely with the contractor management staff, based in the same office, to find the best design, procurement and programme solutions as we negotiate pre-award and over the whole life of the job.”
McCullough admits this is management-intensive, but says the advantages include the ability to draft in skills more quickly, the opportunity to cherry-pick contractors’ contacts, and the creation of a hybrid modern structure to attract younger skilled recruits.