They are common in Asia in cities such as Hong Kong and Singapore. They are coming to European metropolises such as Munich and Paris. But they have proved elusive in the UK. “They” are multi-storey sheds and, so far, just one example has made it out of the ground: Brixton Estates’ ill-fated 234,000 sq ft double-decker X2 at Heathrow, which earlier this year was finally fully let, eight years after completion.
The spotlight has fallen on the concept once again with Amazon’s announcement this summer that it will take 2.2m sq ft in a four-floor building at Roxhill and Port of Tilbury’s London Distribution Park. The internet giant is actually following in the lesser-known footsteps of freight distributor Uniserve, which in 2014 won planning consent for a similar structure for its own use at Clickett Hill Road, near the port of Felixstowe, and, if built, would be a whopping 131ft high.
Logistics experts argue that these single-operator, cargo-lift-served buildings aren’t multi-storey sheds in the truest sense, but there seems to be no doubt that more multi-level warehouses will be built in the UK. The question is when they will appear.
Andy Gulliford, chief operating officer at SEGRO, which inherited X2, says: “My take is that multi-level buildings will come in places where there won’t be a choice – in inner-ring urban areas. I can’t see it working on a site next to a motorway junction.”
Overcoming tenant resistance will be a key hurdle if more multi-storey buildings are to succeed. “The minute you try and transport a global parcels operator to a multi-storey building in the UK, even though they seem happy with it in Singapore and Hong Kong, the almost immediate response is ‘no thanks’ because they are used to operating in local market conditions,” reports Richard Sullivan, industrial and logistics director at Savills.
This chicken-and-egg situation may explain why developers have politely declined sites offered with a potential for multi-storey shed use, says Montagu Evans’s industrial and logistics partner, Jody Smith. “Initially they may find it hard to fund the build cost. But if one developer goes ahead, others may follow,” he says.
A key consideration for a UK developer will be whether to provide ramp access to the upper levels, particularly as those built to take 44-tonne HGVs need to be both large and sturdy. The answer, suggests Seth Love-Jones, partner at Tuffin Ferraby Taylor, may be a more modest structure. He explains: “At city centre sites the demand is for smaller delivery vehicles doing last-mile deliveries. The average man-and-a-van doesn’t need full dock-levelled loading. But with ramps and access to mezzanine and first-floor levels, a small multi-level shed can easily double the number of loading points. If a sophisticated traffic management solution is implemented, far better efficiency can be achieved.”
Even if the concept is sound, developers want reassurance that investors will, literally, buy into it. Savills’ Sullivan admits: “The challenge for the industry is how to value these buildings so that they can be traded. Somebody has to take a big leap of faith to provide the evidence that creates comparables.”
As land values in urban areas continue to rocket, largely due to competing residential use, that leap may now not be that far off – market opinion suggests we can expect to see one or more new-generation multi-storey buildings, probably in London, by 2020.
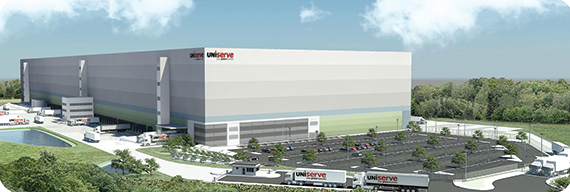
Multi-level vs multi-storey
Must a multi-storey warehouse have a ramp for vehicle access to the upper floors? That depends, says Jason Fong, Hong Kong-based Asia Pacific research manager at CBRE. “Ramp-up buildings will have higher throughput but lower area efficiency as some of the site area is used by the ramp itself. Cargo-lift buildings are cheaper to build and can be constructed in smaller site areas. However, the throughput suffers as all goods on the upper floors must be transported via elevators.”
Some UK logistics market commentators suggest that cargo-lift buildings should really be described as multi-level, but all are agreed that true multi-storey buildings will have permanent upper floors.
So where does that leave Amazon’s future Tilbury warehouse? “That is a single-storey shed with structural mezzanines,” reckons Charles Binks, head of logistics and industrial at Knight Frank, explaining that the upper floors are designed to be removable, should another tenant occupy the building at a later date.
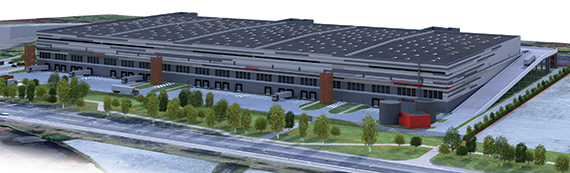
Lessons from mainland Europe
It may be politically sensitive to suggest that the UK might pick up a tip or two from other European countries, but in the case of multi-storey sheds it would be good advice. Luxembourg-headquartered private property investor Compagnie des Parcs has developed several multi-storey buildings in Switzerland, and London-based sister company Compagnie du Parc is considering doing the same in the UK.
“As we get to acquire land in inner London, at some stage it will become economically viable to construct such a building,” says managing director Jonathan Coenca. He thinks it is likely that a start could be made within the next two years, with completion by 2020.
SEGRO chief executive Andy Gulliford won’t be drawn on when his company might put a spade in the ground for a multi-storey building in London, but the company is already under way with two such facilities in Germany and France. First out the ground will be a 150,000 sq ft two-storey spiral-ramp warehouse in central Munich for a single unnamed internet retailer client. Next year Gulliford hopes to start on the DC7 scheme at Gennevilliers, northern Paris, where SEGRO has already prelet half of a two-storey 700,000 sq ft shed with a straight two-way ramp.
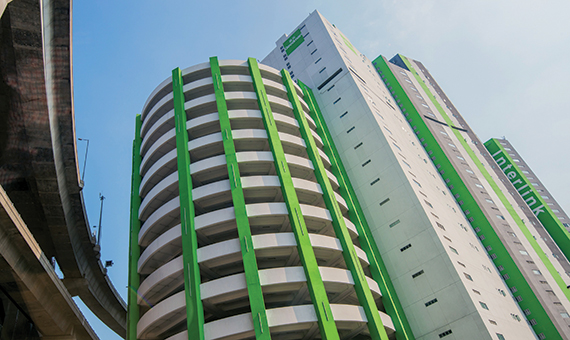
Lessons from Asia
Anyone considering developing a multi-storey warehouse in the UK needs to be aware of three key issues, says Jason Fong, Hong Kong-based Asia Pacific research manager at CBRE.
Building specifications
“Design will be more complex as building upwards is a different ballgame from constructing single-storey sheds. Loading and height capacities will be different,” says Fong. He adds that there are constraints in clear ceiling height when building multiple storeys, but the trade-off is more usable floor area in total.
Management of multi-storey facilities
Because multi-storey facilities typically have more than one tenant, there is an additional learning curve in the design and management of the building. Fong notes: “Efficient sharing of common facilities and cost allocation among multiple tenants will need to be taken into consideration.”
Multi-storey types
For markets that are starting to explore multi-storey warehousing, such as the UK, Fong suggests that buildings should include ramps from the outset, rather than adopting a cargo-lift model (see box, previous page) then moving to a ramp later. He explains: “The increased efficiency of the ramp-up facility can better suit future technology changes in the industry and is more relevant to the modern logistics occupier.”
Planning issues
Logistics experts suggest that if multi‑storey sheds have a future in the UK they will need to be located near to city centres. But would they ever get planning consent in such locations? The visual impact alone of a 65ft-tall (or higher) logistics structure may raise the eyebrows of local planners, points out legal planning expert Claire Fallows, partner at law firm Charles Russell Speechlys: “The closer you get to urban areas, the trickier it’s going to be.”
She says that vehicle access and noise will need to be carefully thought through to minimise the impact on a scheme’s neighbours: “Typical issues for large warehouses are rights of light and amenity to nearby properties and these will be amplified in urban areas.”